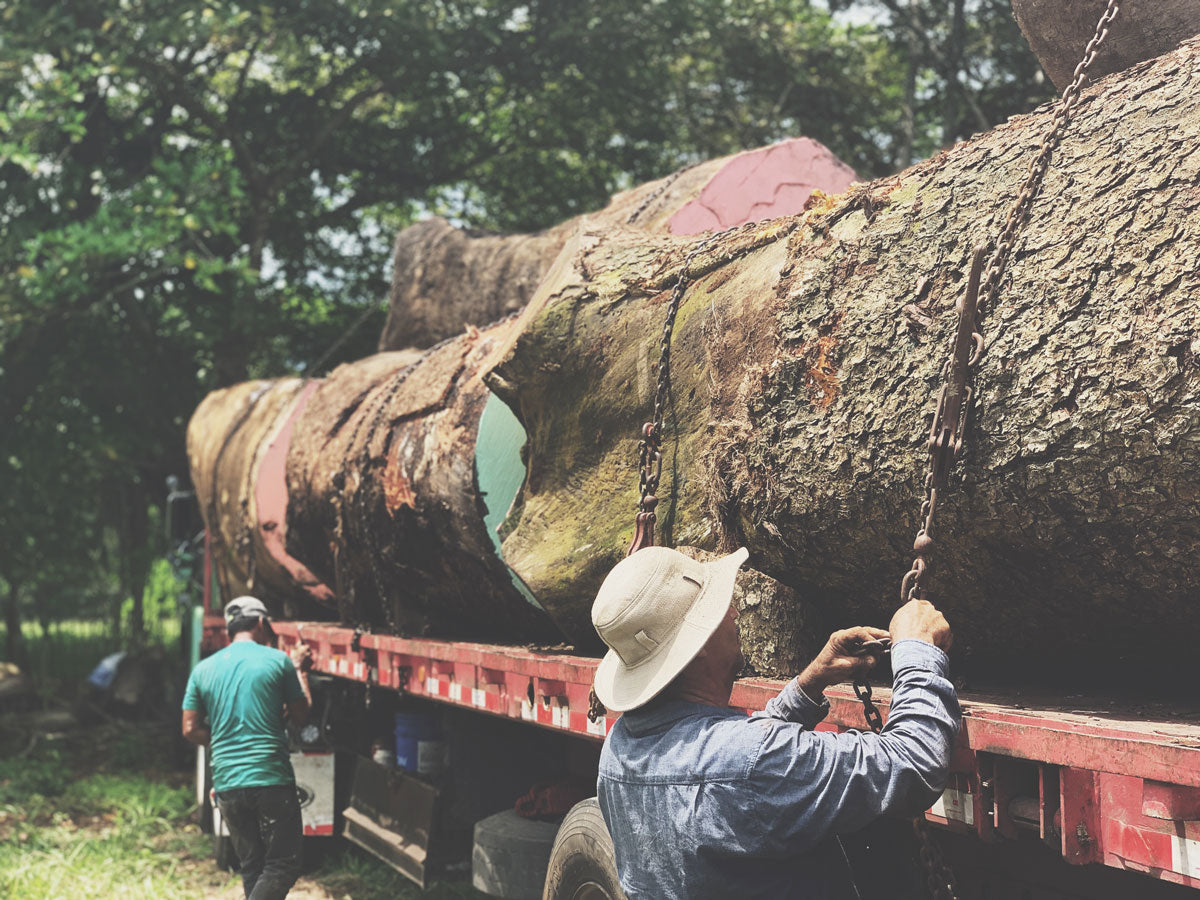
The MINAE (Ministry of Environment) conducts an examination of the designated area, and based on the outcomes, they may either grant or deny approval for tree harvesting. In the event of approval, MINAE stipulates a specific percentage of trees per hectare (10,000 m2) that are permissible for harvesting. Our founder, Bernardo Urbina, personally engages in the selection and approval process for Monkey pod and Parota logs, which he procures from local farmers situated in the rural regions of Costa Rica. Subsequently, following governmental approval and completion of requisite paperwork, the acquisition of a "yellow tag" permit is secured to facilitate the transportation of the logs to the mill.
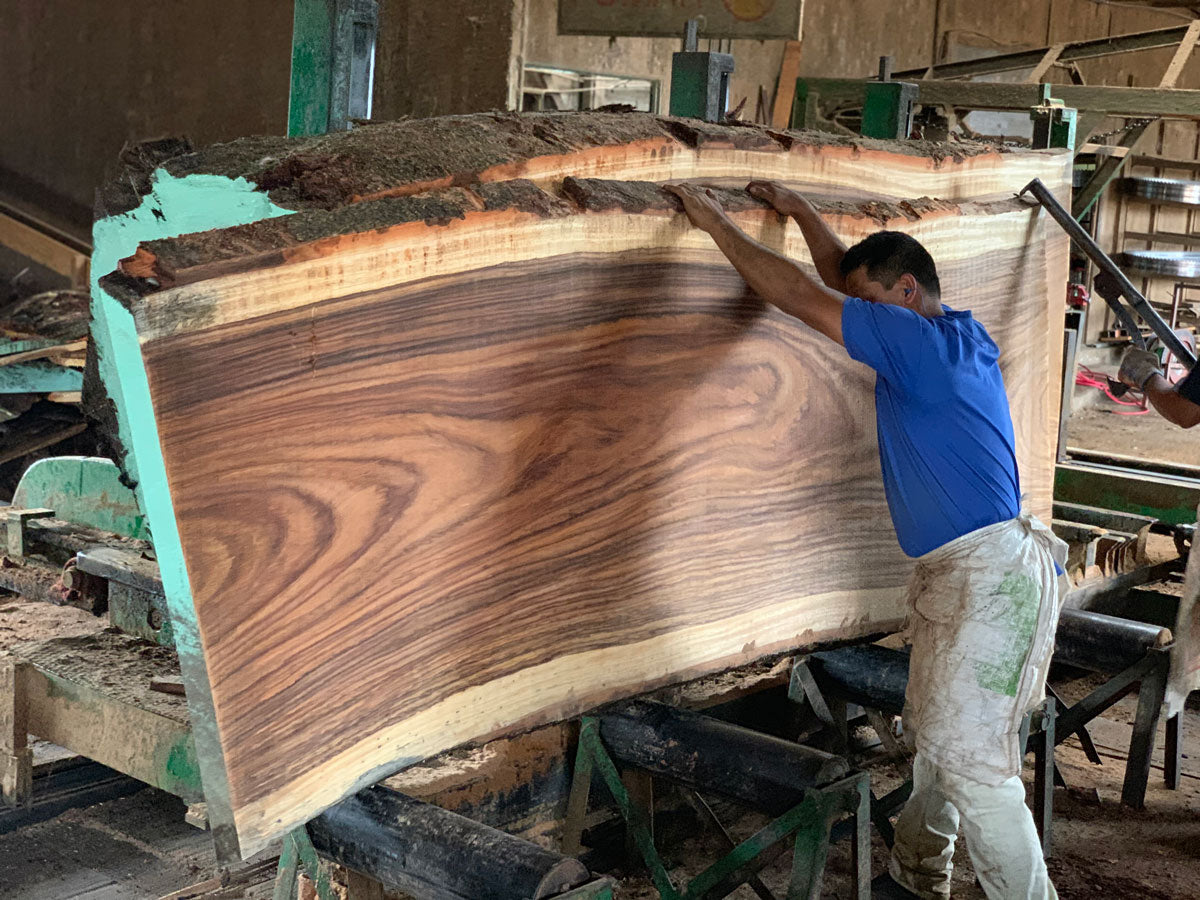
Following the loading of Monkey pod and Parota logs onto the cargo truck, each accompanied by its corresponding "Yellow tag," we proceed to transport them to the Mill.
Upon arrival at the Mill, we undertake the unloading of the logs, conduct a meticulous inventory check, and assign a distinct number to each Monkey pod and Parota log, categorizing them based on their size and species. Bernardo Urbina, along with his team, deliberates on the optimal approach for milling each log, ensuring the production of unique slabs. Subsequently, as the slabs are processed, they undergo stickering in preparation for their transfer to the warehouse, where the kiln is located.
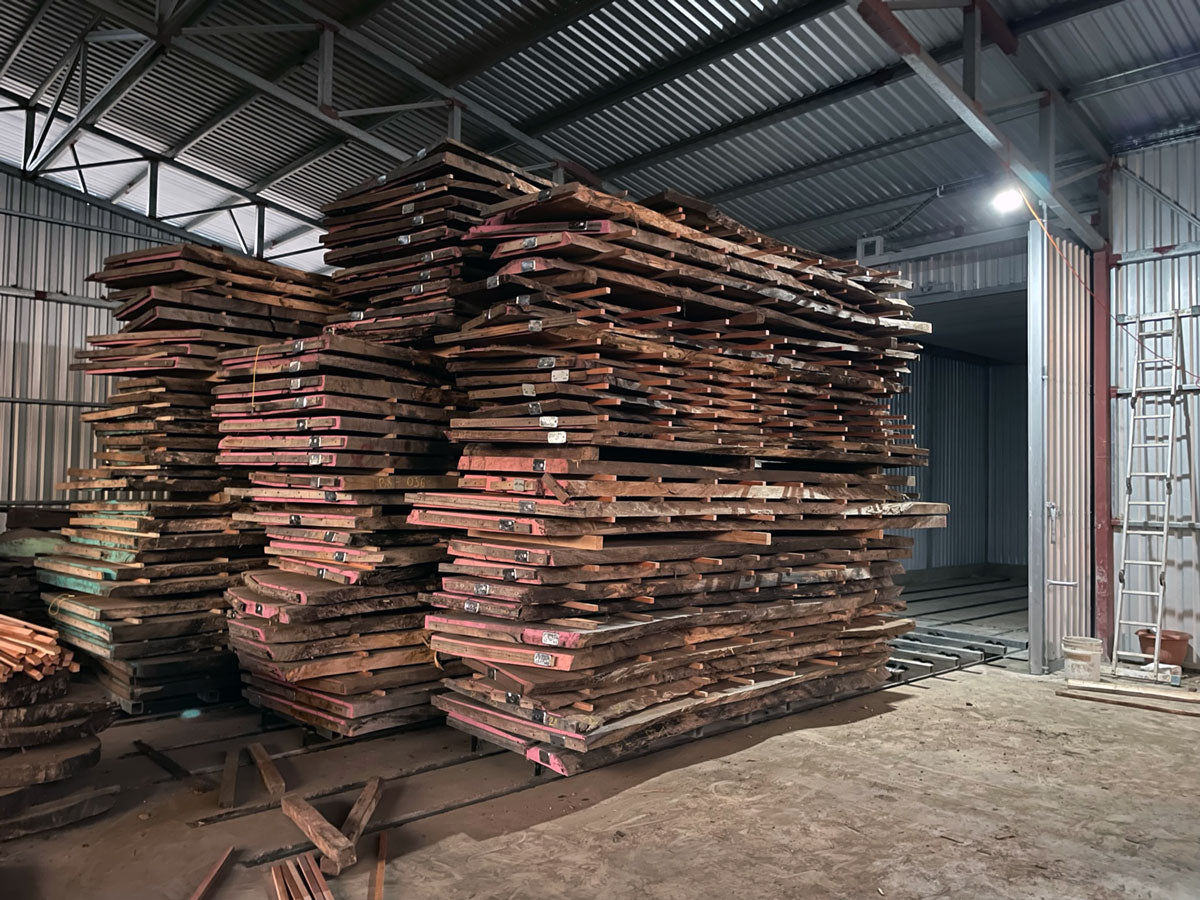
Upon arrival at the warehouse, Monkey pod and Parota slabs undergo a meticulous organization process based on size, species, and thickness. Each slab is methodically stickered, maintaining a spacing of 12-16 inches, and undergoes a pre-drying phase lasting 1.5 months before progressing to the kiln. Our kiln infrastructure comprises three carts, each with a capacity of 15 tons, facilitating the drying of 30 slabs per cart—amounting to a total of 90 slabs.
The kiln operates using sophisticated Italian software, integrating four strategically positioned sensors on the slabs to monitor their current moisture levels. Additionally, the system incorporates relative humidity sensors within the kiln, four exhaust flaps, four bidirectional fans, and an extensive 12-meter-long stainless steel heating source. These components collaboratively function, both synergistically and wirelessly, adhering to a meticulously designed computer program. This program ensures a gradual and efficient drying process, aligning with our predetermined moisture content specifications.
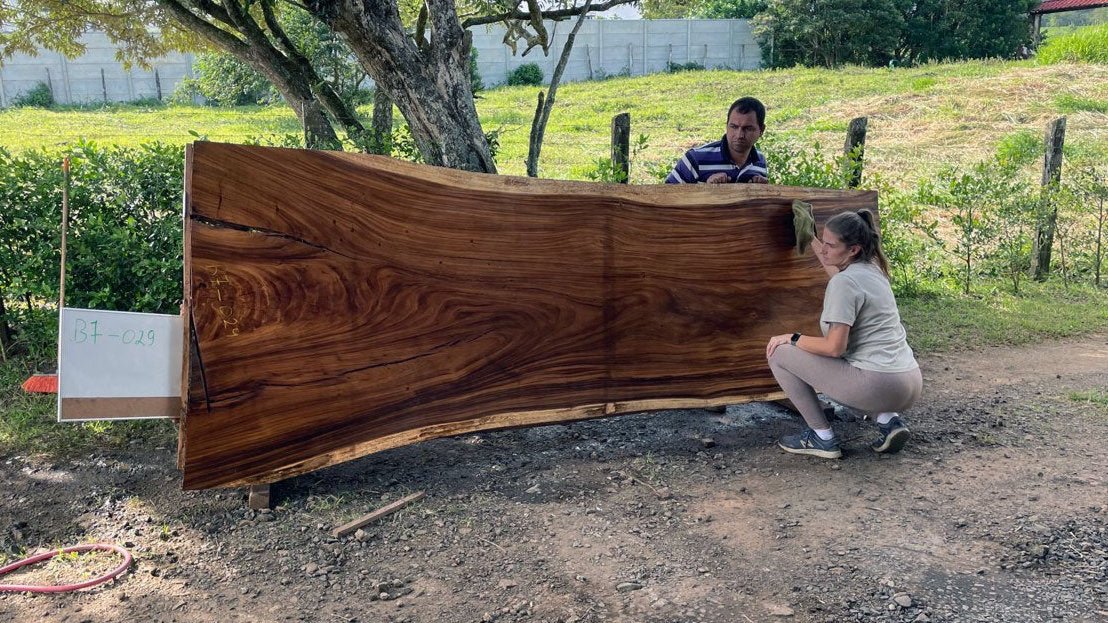
Upon completion of the drying process for Monkey pod and Parota slabs, we meticulously sand them down to a 120-grit finish. This crucial step reveals the distinctive and aesthetically pleasing grain patterns that were previously concealed. The application of a small amount of water enhances the visual appeal, providing ample time to capture the authentic appearance of the slab before the final finishing.
Simultaneously, each slab undergoes comprehensive documentation, resulting in the creation of a unique code. This coding system ensures a traceable record, enabling us to correlate each slab with the corresponding image captured during documentation. This streamlined tracking mechanism not only facilitates the efficient shipment of slabs to our warehouse in the US but also expedites the uploading process to our website, ensuring the representation of every kiln-dried slab that undergoes export.
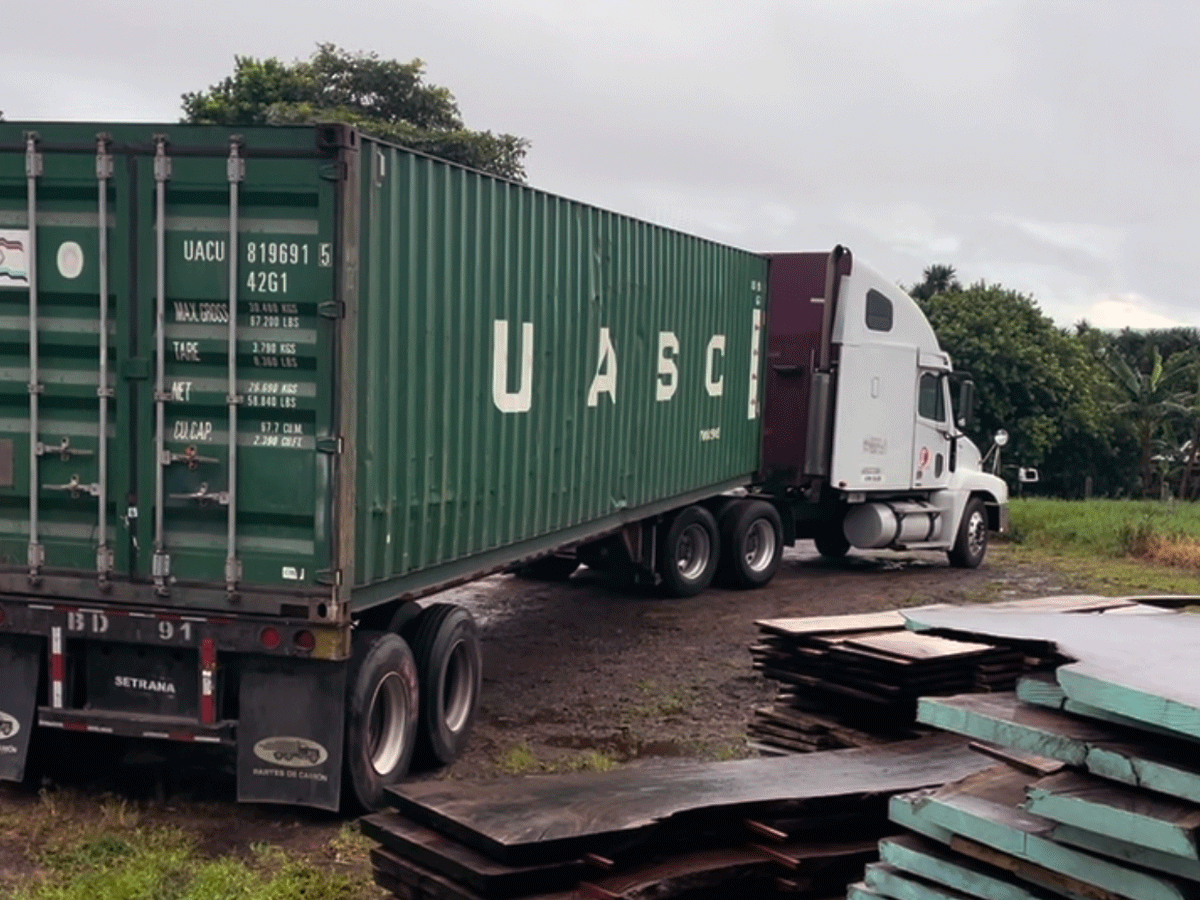
As our inventory in the United States approaches the 50% threshold, we initiate the final stages of shipping. This strategic approach aims to preempt any potential shortage of slabs for our clients, ensuring a continual rotation of Monkey pod and Parota offerings. In collaboration with our logistics partner, we orchestrate the container booking process and meticulously prepare each slab by cleaning and thoughtfully loading them. To enhance safety during transport, the slabs are securely strapped in sets of five to mitigate the risk of damage.
Following the loading phase, officials from both the Ministry of Environment (MINAE) and the Fito Sanitary department conduct comprehensive procedures. These include fumigating the container and conducting a thorough inspection to verify alignment with the manifest. This rigorous protocol is integral to regulating the extraction and exportation of wood, thereby preventing illegal activities. Subsequent to this meticulous process, the container embarks on its journey to our warehouse.
The MINAE (Ministry of Environment) conducts an examination of the designated area, and based on the outcomes, they may either grant or deny approval for tree harvesting. In the event of approval, MINAE stipulates a specific percentage of trees per hectare (10,000 m2) that are permissible for harvesting. Our founder, Bernardo Urbina, personally engages in the selection and approval process for Monkey pod and Parota logs, which he procures from local farmers situated in the rural regions of Costa Rica. Subsequently, following governmental approval and completion of requisite paperwork, the acquisition of a "yellow tag" permit is secured to facilitate the transportation of the logs to the mill.
Following the loading of Monkey pod and Parota logs onto the cargo truck, each accompanied by its corresponding "Yellow tag," we proceed to transport them to the Mill.
Upon arrival at the Mill, we undertake the unloading of the logs, conduct a meticulous inventory check, and assign a distinct number to each Monkey pod and Parota log, categorizing them based on their size and species. Bernardo Urbina, along with his team, deliberates on the optimal approach for milling each log, ensuring the production of unique slabs. Subsequently, as the slabs are processed, they undergo stickering in preparation for their transfer to the warehouse, where the kiln is located.
Upon arrival at the warehouse, Monkey pod and Parota slabs undergo a meticulous organization process based on size, species, and thickness. Each slab is methodically stickered, maintaining a spacing of 12-16 inches, and undergoes a pre-drying phase lasting 1.5 months before progressing to the kiln. Our kiln infrastructure comprises three carts, each with a capacity of 15 tons, facilitating the drying of 30 slabs per cart—amounting to a total of 90 slabs.
The kiln operates using sophisticated Italian software, integrating four strategically positioned sensors on the slabs to monitor their current moisture levels. Additionally, the system incorporates relative humidity sensors within the kiln, four exhaust flaps, four bidirectional fans, and an extensive 12-meter-long stainless steel heating source. These components collaboratively function, both synergistically and wirelessly, adhering to a meticulously designed computer program. This program ensures a gradual and efficient drying process, aligning with our predetermined moisture content specifications.
Upon completion of the drying process for Monkey pod and Parota slabs, we meticulously sand them down to a 120-grit finish. This crucial step reveals the distinctive and aesthetically pleasing grain patterns that were previously concealed. The application of a small amount of water enhances the visual appeal, providing ample time to capture the authentic appearance of the slab before the final finishing.
Simultaneously, each slab undergoes comprehensive documentation, resulting in the creation of a unique code. This coding system ensures a traceable record, enabling us to correlate each slab with the corresponding image captured during documentation. This streamlined tracking mechanism not only facilitates the efficient shipment of slabs to our warehouse in the US but also expedites the uploading process to our website, ensuring the representation of every kiln-dried slab that undergoes export.
As our inventory in the United States approaches the 50% threshold, we initiate the final stages of shipping. This strategic approach aims to preempt any potential shortage of slabs for our clients, ensuring a continual rotation of Monkey pod and Parota offerings. In collaboration with our logistics partner, we orchestrate the container booking process and meticulously prepare each slab by cleaning and thoughtfully loading them. To enhance safety during transport, the slabs are securely strapped in sets of five to mitigate the risk of damage.
Following the loading phase, officials from both the Ministry of Environment (MINAE) and the Fito Sanitary department conduct comprehensive procedures. These include fumigating the container and conducting a thorough inspection to verify alignment with the manifest. This rigorous protocol is integral to regulating the extraction and exportation of wood, thereby preventing illegal activities. Subsequent to this meticulous process, the container embarks on its journey to our warehouse.
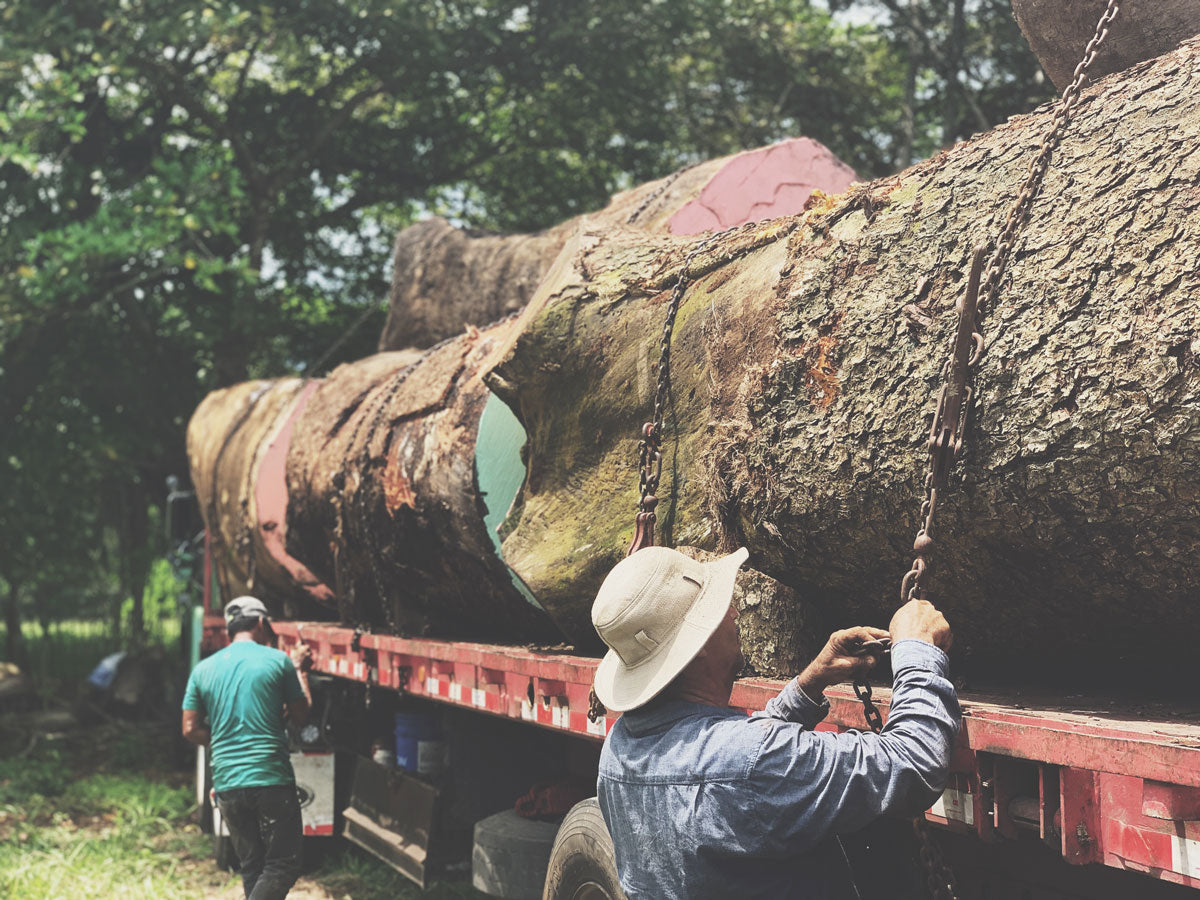
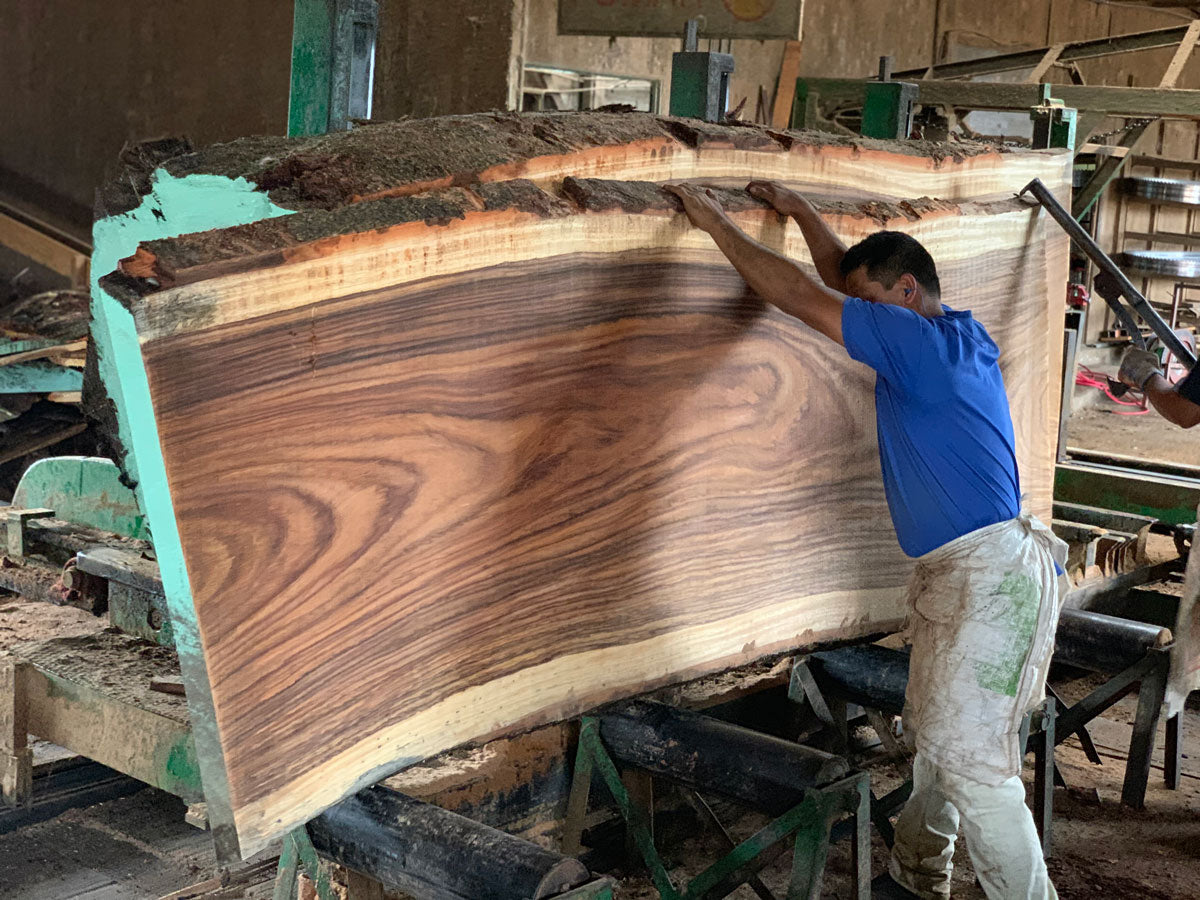
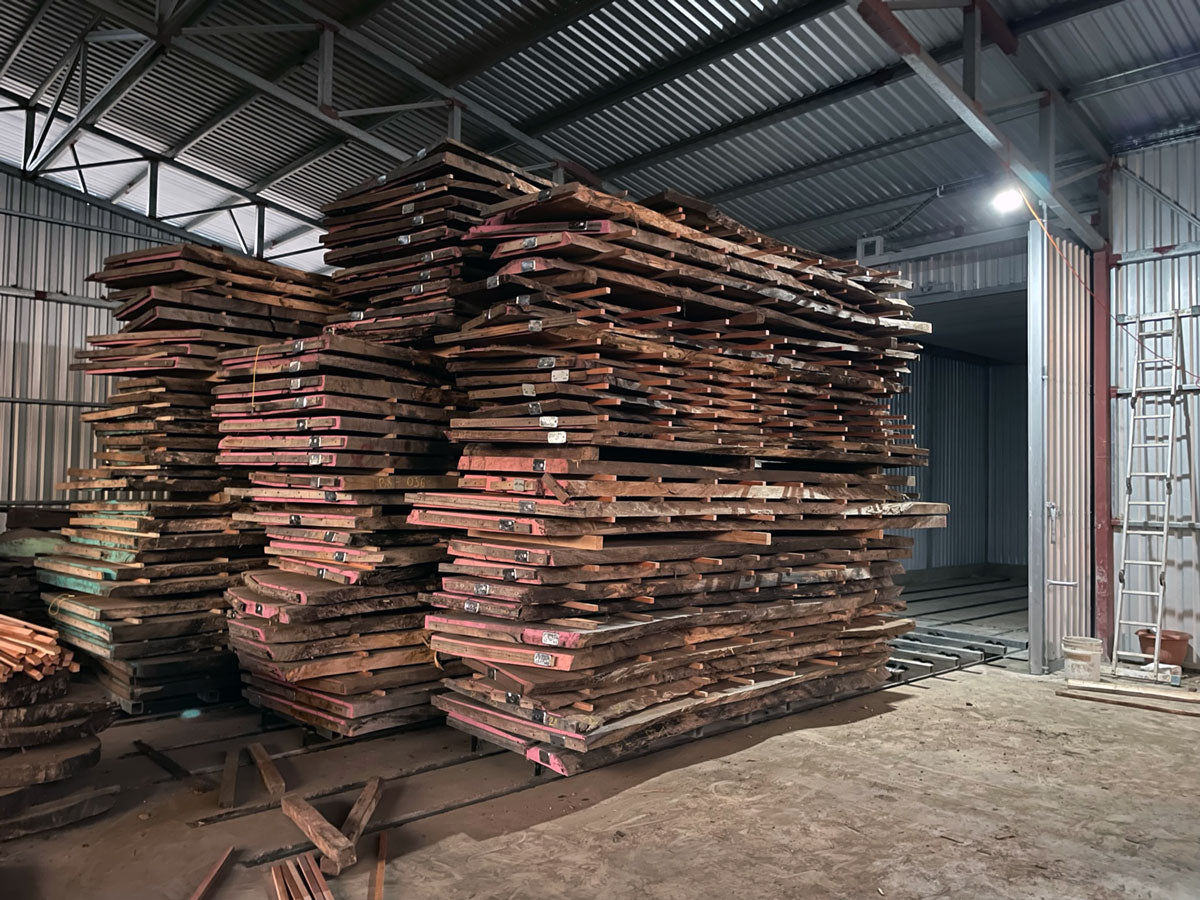
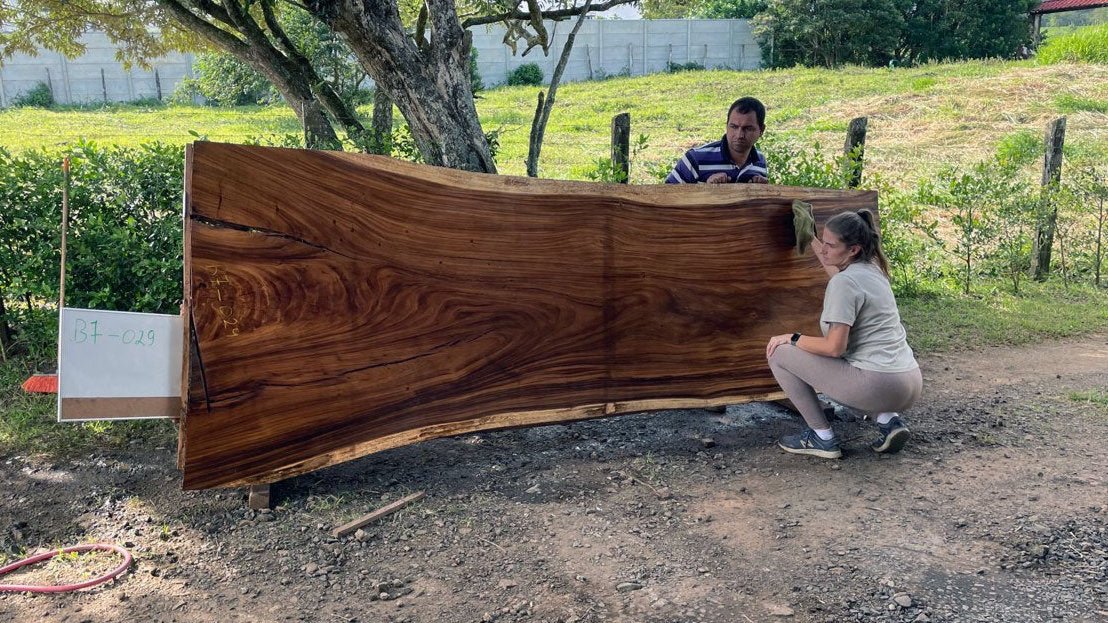
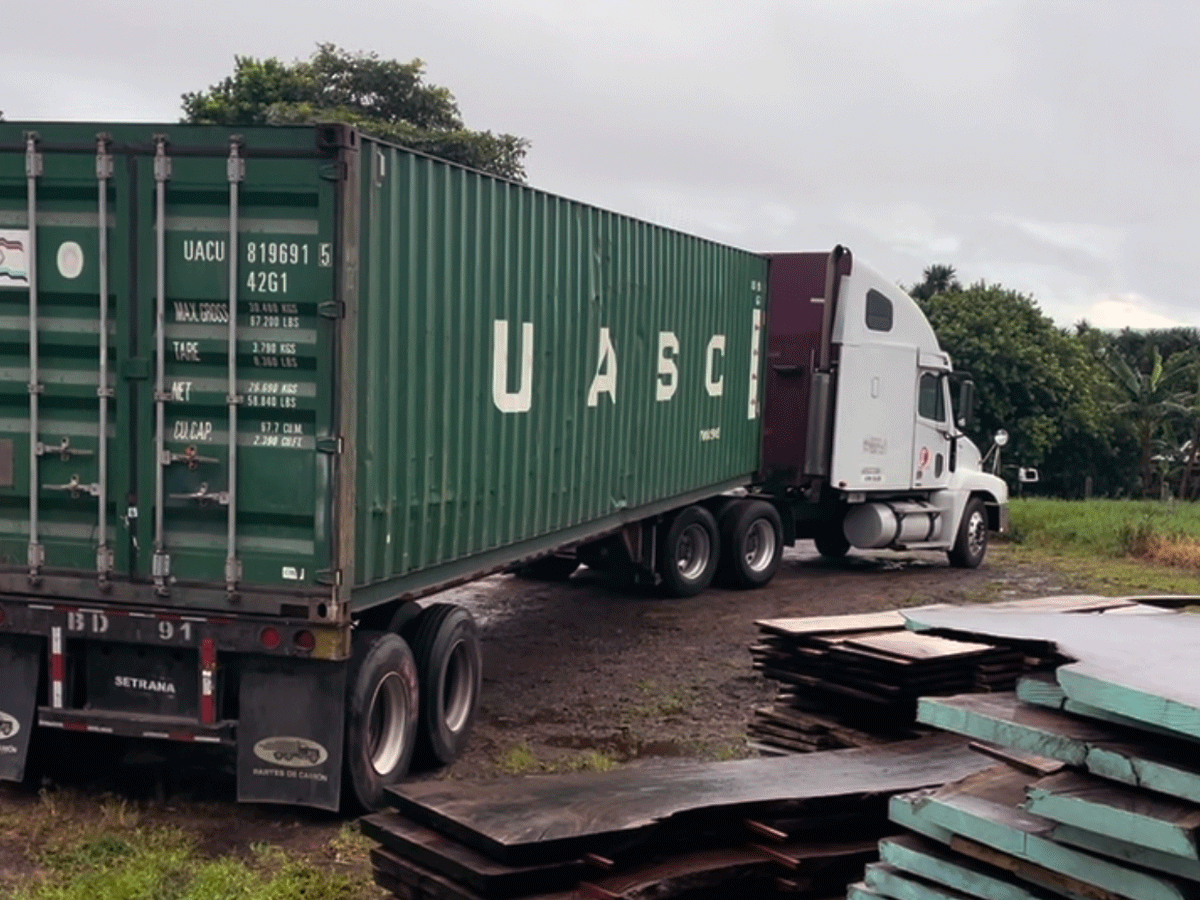